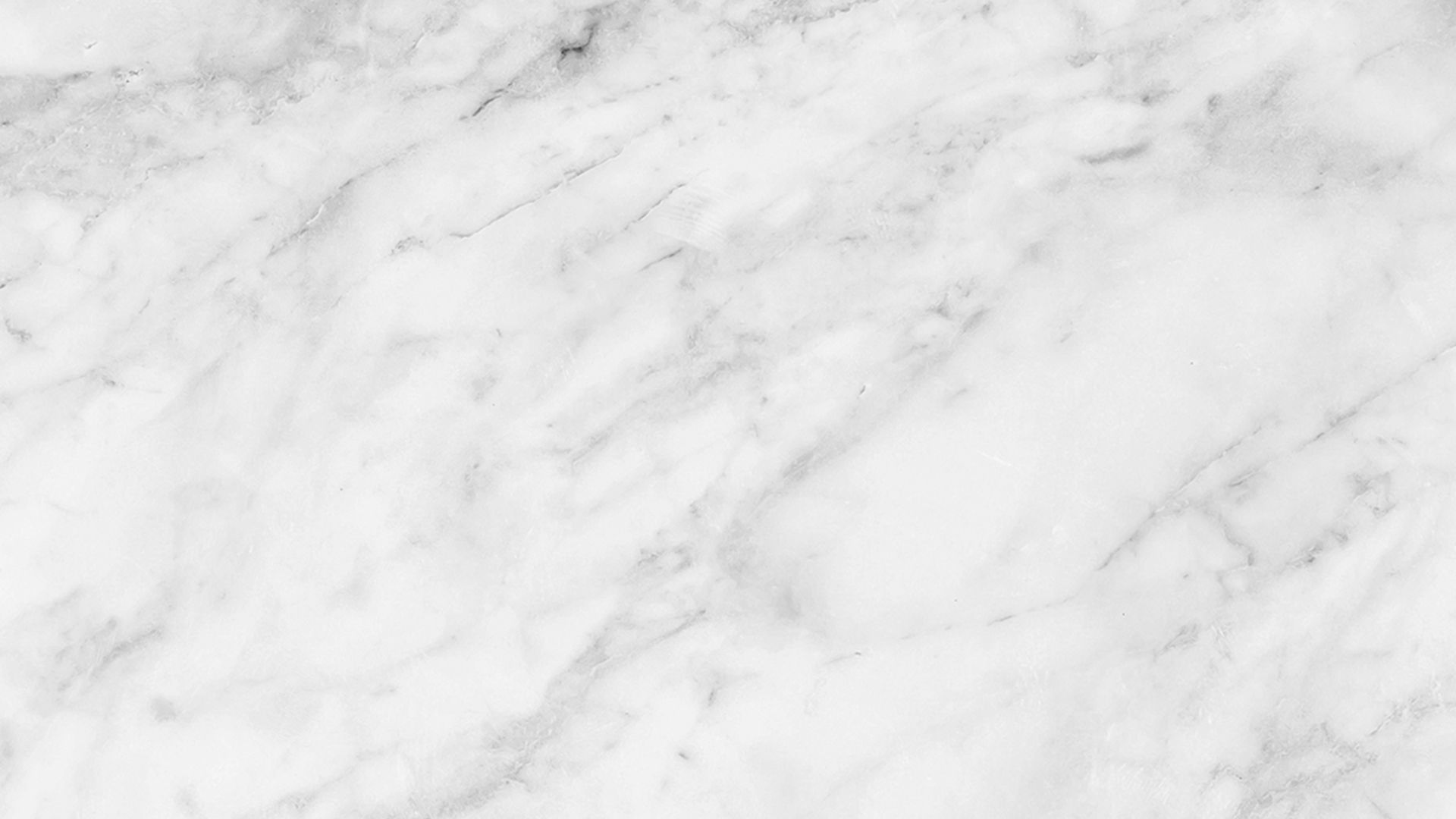

Office: 970-565-2087
Fax: 970-565-7281
​
25716 Road L Cortez, CO 81321
Concrete & Asphalt Recycling
Concrete recycling entails breaking, removing and crushing concrete into a material of a specified size and quality. Sidewalks, building columns or foundations are broken up and compiled. The concrete can either be hauled to a recycling site for crushing or crushed on-site using a portable crushing rig. 
​
Advances in equipment, such as crushers with magnets, allow steel remnants to be removed with less manual labor, so materials ranging from jointed plain pavement, to jointed reinforced pavement, to continuously reinforced pavement can all be crushed and recycled.
​
The crushed concrete and asphalt is used to produce recycled aggregate (stone base) for new roads, parking lots, driveways, patios and more.
​
Asphalt recycling entails asphalt chunks or millings being mixed in an asphalt re-cycler along with some water and additives. For hot mix asphalt, the mixture is tumbled and heated for approximately 20 minutes before it is ready for use. Cold recycling, on the other hand, avoids the use of heat and saves energy in the process. Often the asphalt cement (the glue that holds the pavement together) retains its adhesive capabilities and can be reused as a binding agent. Fine mineral particles that are generated in the process of producing the asphalt pavement material may also be reused which helps to conserve natural resources.
​
Asphalt recycling provides a profit or savings potential of $30.00 to $80.00 per ton.
​
According to the Federal Highway Administration, over 80 percent of asphalt removed from roads is recycled. Recycled asphalt product is now routinely accepted in asphalt paving mixtures as an aggregate substitute and as a portion of the binder in nearly all 50 states. . 
​
In addition to asphalt and concrete, D & L Construction can crush rock, cement blocks and other concrete products.
​
The recycled aggregate is available to contractors for pick-up or delivery.
​